Recent severe winter weather in Texas has created a call to action for power and natural gas producers. Voters are demanding action that translates to reliability of electric power to their homes and businesses. The organizations in charge of the reliability of these plants have offered the same advice for well over 20 years. Facilities continue to freeze up. Einstein defined insanity as “..doing the same thing over and over and expecting different results”. These plants continue to use the same methods to freeze protect their facilities. And it continues to not work.
Why did we lose power?
Several causes have been listed for that loss of power, and two primary facility types have been most consistently blamed for power outages, Gas Plants or Midstream Companies and Power Plants. Loss of Power is the number one cause of gas facilities shutting down, and one of the most common causes for Power Plants going down is…a lack of natural gas.
For as long as power plants have been creating power, and midstream companies have been sending natural gas to power plants, freeze ups have been an issue within these facilities. The solution to the freeze ups is the same as it was 20 years ago. The advice provided and technologies available to these plants is the same as it has alway been. It just does not work.
Preparation at the facility level
Go to any gas plant/midstream company in charge of sending natural gas down the line, and see if the person in charge feels like they are prepared for winter. Do the same of any of your local power plants. They will all tell you “yup, we’re good to go”. I know because I make a living doing just that.
Here’s the issue. When they say that they are ready to go, they mean that they comply with the directions given to them from their bosses, who in turn have complied with regulating agencies and advisors like ERCOT, TexasRe, Texas PUC, The Texas Railroad commission, and even The Texas Oil and Gas Association.
Each of them have provided guidelines for proper preparedness, and not one single piece of advice is different from any other winter, ever. Major freeze ups were documented many times in the recent past.
Some examples of preparedness suggestions can be found on each site:
Texas Public Utilities Commission:
Recommends that plant maintenance personnel fix failed equipment, and be sure that past solutions are “adequately” installed.
Texas Railroad Commission:
Has designated some midstream companies and certain critical feed points as vital. No specific suggestions on how to keep running if they freeze though…
ERCOT:
For many years ERCOT has has put on workshops for power plant maintenance teams in the winter season. Hosted every September, their winterization workshops have been well attended. ERCOT has also sent their personnel on random plant audits through the fall to check and see how well plants were prepared. One example here from 2015 workshop.
TXOGA
More recently, the Texas Oil and Gas Association has stepped in to encourage it’s midstream members to really give it their best and prepare for the winter with a set of ideas and suggestions on how they could best be prepared for the winter and stay on line:
Dozens of other subject matter experts have offered similar advice:
It’s a global warming and Texas Grid ego issue.
CPS energy had the same issue in 2011, and spent $ 20 million fixing their freeze up issues. No different 10 years later, they followed the same advice with insulation, heaters and temporary enclosures…exactly what ERCOT recommends.
The mechanical experts at ASME even chimed in by stating that facility managers just didn’t learn their lesson from 2011, then throwing out facts and figures like how much money was lost and how many Texans were without power. They just say that the power went “off line”.
So a common thread exists in both the solutions recommended, and the accusation that those responsible neglected to be prepared. A third issue is that elected officials and government agencies are qualified to create a good solution… but let’s not go down that path.
Efficiently Inefficient
One of the most common recommendations consistently provided by any of these agencies offers the solution of building a temporary shelter around key components that cannot be heat traced or insulated. Many of these components need to be accessed frequently, or are too small for heat trace to do a really effective job protecting them.
Temporary enclosures, walls or “hooches”, as they are called at the plant, are one of the biggest problems when it comes to freeze ups.
First is the belief that a thin plastic wall can somehow protect critical instruments and valves. From the most current Texas Oil and Gas Association list of things to do to protect your gas plant from freezing up, they posted the following on their website:
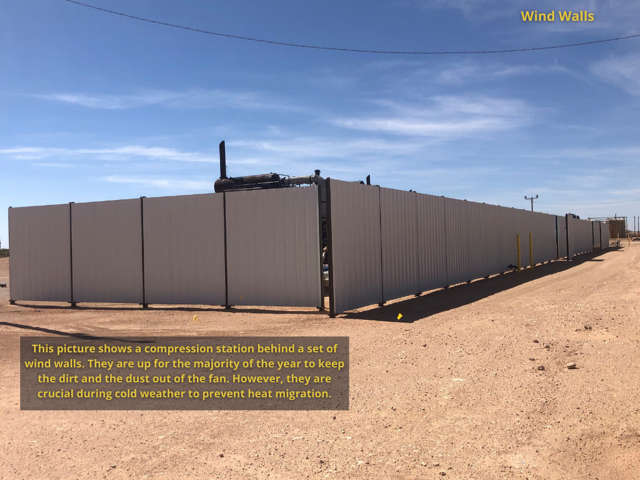
How can a wall prevent heat migration??
Wind break recommendation by ERCOT back in 2015:
So if walls don’t heat…how do we keep it warm, so that it doesn’t freeze?
Improperly protected critical devices are nearly 100% to blame when freeze ups occur in both gas and power plants. It is a fact that many small inexpensive components are the culprits of a large majority of the freeze ups in years past.
Finally, it’s not the assumption that putting a tarp or wall around a set of critical devices that is bad, but the lack of direction and misguided information put out that tells a plant facility manager how to heat those enclosures.
Heat is needed to keep these enclosures warm. None of the advisors really tell plants how exactly they are supposed to accomplish this. Some suggestions are:
Kerosene or Multi Fuel Heaters
Portable lamp and milk house heaters:
While these heaters all will create heat, there are several key issues with using them-
BTU Ratings and R Values– these heaters are not designed to heat an enclosed temporary hooch. You need to know how much heat is required to do the job. Also, the walls are not insulated, no R value has been considered. The enclosure will not be well insulated.
In normal terms, if you are planning to take a trip in a car that is 100 miles in distance, and your car gets 25 miles to the gallon- you need to be sure to have at least 4 gallons of gas…right?
If you have an enclosure made of plastic around your duct burner system at a natural gas fired power plant- and that enclosure is 12 ft wide x 20 ft long by 8 ft tall- that space needs a specific amount of heat within it to perform the task.
No such considerations are made when designing these hooches.
Heated closures vs. heated components
A much better approach would be to heat each critical component within that enclosure with its own heater.
It has not been done before because no such product existed.
Powerblanket offers a new and unique solution for many of these key components and a way for most plants to eliminate these heated enclosures.
Non heat traced components can now effectively be protected thanks to products recently developed by Powerblanket. Valves, transmitters, pumps, and small tanks all can be individually covered and protected while meeting Class 1 Division 2 requirements.
There is no longer any need to build ineffective and dangerous tarps around critical non-heat traced components. Recently developed product offerings for heating valves, transmitters, pumps, pipes and many other components offer solutions to these problems that have never been offered before.
Powerblanket Hot Boxes integrate heat and Class 1 Division 2 rated safety, and can be made to fit a wide variety of sizes:
Powerblanket Valve and Transmitter Box Heaters can fit right over key valves and actuator systems to keep that valve control performing throughout that cold winter snap:
Dozens of other possible sizes and configurations can be created exactly for your application.
Heaters by Powerblanket can be designed to run on either 120,208 or 240 volts ac and can maintain up to 180 F while being exposed to up to 400F.
Powerblankets are 100% made in the USA in Salt Lake City, Utah. 100% customizable and can be rated for use in Class 1 Division 2 areas. Safe, effective and fit to your application.
Curious to see how Powerblanket can meet the unique needs of your industry?