When pouring concrete in cold weather, temperature protection is critical. Dropping temperatures and wet elements will lengthen the curing time of concrete and create costly delays while waiting for it to set. Delays virtually always lead to you losing money, so it’s imperative you find a solution to help your concrete set faster when the weather says otherwise.
The American Concrete Institute defines cold weather concreting as:
“A period when for more than three successive days the average daily air temperature drops below 40° F and stays below 50° F for more than 21 hours.”
Low temperatures means concrete takes longer to set due to moisture being trapped in the concrete. This is because cold weather prevents evaporation of the water in the concrete mix. The faster the water evaporates, the faster the concrete hardens. The less water evaporates, the longer the concrete will sit there before curing completely.
How Long Does Concrete Take to Set?
The length of time concrete takes to set depends on if additives were mixed into the concrete, but generally it takes 28 days. At that point, concrete is considered fully set, but in reality concrete never stops curing. Concrete that hasn’t reached 28 days can still be walked on starting at 48 hours after pouring, and will reach 70% of compressive strength after 7 days.
What temperature is too cold to pour concrete?
In normal conditions, laying concrete in cold weather is best done when the air temperature is between 50-60°F. Try curing below that, and the water within the concrete will begin to freeze, weakening the overall strength of the concrete.
What happens to concrete if it freezes?
In addition to taking longer to set, water that freezes in the concrete will inevitably lead to cracking. Though all concrete is expected to crack over time, it can be controlled and guided when setting within the ideal temperature range for curing. Frozen concrete leads to uncontrollable cracking, and must be mitigated by providing heat to the concrete in the early stages of curing.
What Options are there for Cold Weather Concrete Curing?
There are a number of options out there when laying concrete in cold weather to help it cure when the temperature isn’t in your favor:
- Chemical additives: additives in liquid or powdered form are added to the cement mix in order to better control hardening.
- Concrete curing blankets: these blankets create a layer of heat above the concrete, allowing water within the concrete mixture to evaporate faster and increase curing time without compromising durability.
- Hydronic heating systems: heated propylene glycol keeps curing concrete at stable, even temperatures.
- Poly/tarp cover with forced air heat applied: insulated tarps cover the concrete to keep cold out, while an attached heating unit blows hot air across curing concrete.
Costly cold weather consequences
In some situations, there is the luxury of project postponement in favor of better climate temperatures. In most cases, however, schedules and deadlines make it necessary to place concrete in less than favorable conditions. Penalties and fines for not meeting defined schedules can be the difference between a profitable or unprofitable job. In these cases, all factors need to be taken into consideration. Ensuring proper concrete curing while sustaining concrete strength and durability is critical.
How Can I Speed Up Concrete Curing?
Keeping concrete in the warm can be difficult when the temperature is below ideal for setting. However, cold weather can be mitigated if you are prepared to deal with it. The most important thing to remember is that the concrete temperature needs to be kept high in order for the water inside it to evaporate.
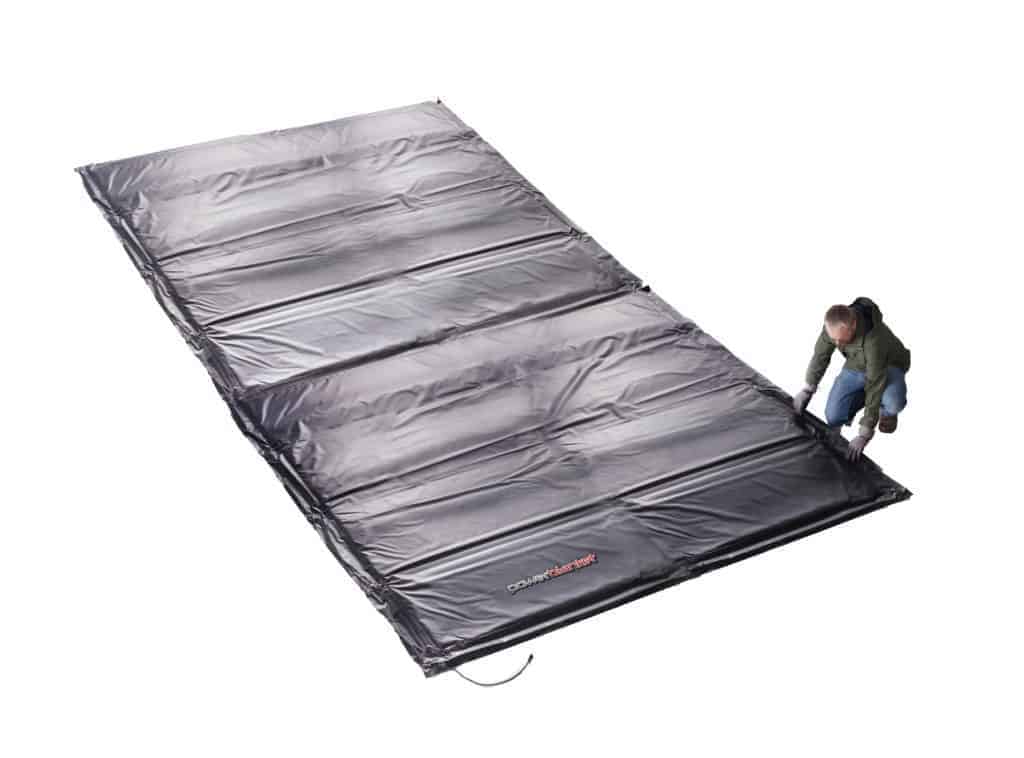
Powerblanket recommends the following tips to protect concrete from frost:
- Use heaters or concrete blankets to thaw surfaces where concrete will be poured. Pouring concrete on frozen ground will quickly cool concrete well below ideal temperatures. Using a heater or blanket to prepare surfaces will prevent too-quick cooling or freezing and help keep the necessary reactions within the concrete going.
- Mix cement using hot water to help increase the temperature of the concrete.
- Store materials in a warm location, or use a portable hot box to maintain materials under a constant temperature.
- Use quick-set cement during cold weather. It may set more slowly than the instructions indicate, but will still harden more quickly than traditional cement mix.
- Mix in additives that accelerate curing time.
- Use extra cement to make the reaction hotter and cause concrete to hydrate more rapidly.
- Utilize squeegees or a vacuum to remove bleed water that has a difficult time evaporating during colder weather.
By utilizing these tips when pouring concrete in the winter, you can prevent damage as a result of freezing at an early stage of cure, maintain development of sufficient strengths in a timely fashion, ensure durability and long-term structural integrity, and keep your project on schedule.
For additional information about cold curing concrete procedures, check out this article about how temperatures impact concrete that is still curing in Nevada’s Hoover Dam.
Concrete curing solutions from Powerblanket
Don’t wait until the last minute to choose a proper heating solution. Concrete curing blankets from Powerblanket are proven to speed up curing time and keep concrete protected while curing.
Cure your concrete faster and better in cold weather conditions with Powerblanket.