How Long Does Concrete Take To Set?
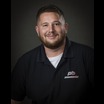
If you really want to know the truth, concrete never stops curing; it continually hardens forever. However, for practical purposes,...
Read MoreIf you really want to know the truth, concrete never stops curing; it continually hardens forever. However, for practical purposes,...
Read MoreWaiting for the curing of concrete can easily test patience, especially when you’re ready to move on to the next...
Read More Experts agree that the best temperature to pour concrete is between 50-60 °F. The necessary chemical reactions that set...
Read MoreIt’s time to answer the age-old question: why does road construction take so dang long to complete? Does it really...
Read MoreWhen pouring concrete in cold weather, temperature protection is critical. Dropping temperatures and wet elements will lengthen the curing time...
Read MorePowerblanket leads the market on industrial heating solutions. If you can build it, haul it, or store it then we...
Read MoreHave you ever been to the Grand Canyon? If so, have you ever been on the Grand Canyon Skywalk? This...
Read MoreBoat Building Epoxy To many people, summer means time on the lake or in the ocean boating or jet skiing....
Read MoreWhen it comes to post curing, maintaining ideal temperature is a must. And if you’re post curing small to medium...
Read MoreWinter weather causes many problems for both businesses and homeowners. One of these problems, however, often go unnoticed until it’s...
Read MoreCustom orders often have the stigma of being time-consuming and laborious. “How long is that going to take?” we ask...
Read MoreAn Atypical Concrete Job Concrete curing in freezers is a unique experience. Walk in freezer concrete floor construction requires a...
Read MoreEven the most expertly-placed concrete will wear with age. Unfortunately, this often means cracking. While this is a nearly unavoidable...
Read MoreLet’s get one thing straight. Plain, gray concrete is best used in military bunkers. Other than that, it’s downright boring....
Read MoreThe word “concrete” most often conjures images of plain grey slabs. While this is certainly the most common form concrete...
Read MoreConstruction crews deal with an added layer of difficulty in the freezing winter months. Tasks that are simple and straightforward...
Read MoreAs motorists travel their daily commute, they appreciate infrastructure upgrades such a freshly paved roads, smoother drives, and improved routes....
Read MoreWhat if we told you that you could speed up curing precast concrete, without the use of any additives, by...
Read MoreTemperature control is vital for businesses that work in the cold. Seeking the right heating solutions for your business leads...
Read MoreConcrete cooling during peak summer heat requires planning, site preparation and some changes in methodology. Hot weather poses many risks...
Read MoreCold Weather Concreting Imagine arriving at the job to find a fresh layer of ice and snow on your pour...
Read MoreConcrete has many advantages over other building materials. It is low maintenance, durable, and forms the foundations of our man-made...
Read MoreWhen it comes to pouring concrete in winter, weather can pose significant challenges. Concrete sets best at 50-60°F; pouring concrete...
Read MorePowerblanket Receives The Association for Manufacturing Excellence Award The Association for Manufacturing Excellence (AME) today announced four recipients of the...
Read MoreFind Powerblanket Products at Heat Authority Heat Authority has researched the leading products for industrial and job-site productivity and offers...
Read MoreHow Warm Does it Have To Be To Pour Concrete? Whether the conditions are hot or freezing, the ideal concrete...
Read MoreHot Weather Concreting Hot weather concreting problems are most often encountered in the summer; however, any condition that increases curing...
Read MoreConcrete cures best at temperatures above 50°F. When ambient temperatures are not warm enough, extra steps must be taken to...
Read MoreReilly Construction out of Wrightstown, NJ, won a bid from the U. S. Department of the Interior to replace the...
Read MoreFirst, let’s define cold weather with respect to pouring concrete. Any time you have three consecutive days where the average...
Read More