Removable Insulation Covers for Industrial Valves – What to Look for
Valve insulation is commonly used to cover petrochemicals products and industrial equipment in the oil and gas industry. Similar to process line piping, valves often must be insulated to minimize heat loss for efficient performance or to keep contents of material passing through the valve at the desired temperature.
Valves are a critical part of any industrial or commercial process. Fluid needed to make things run right in your facility is pushed through these valves quickly and efficiently. At times, these valves are exposed to severe winter conditions or low temperatures that thicken fluid viscosity or even freeze, preventing fluids from reaching critical systems. This in turn causes processes to be shut down and products to not be produced, leading to costly delays and frustrated customers.
How Do I Choose a Heating System?
Valve insulation solutions have existed for many years to keep valves from freezing up. Heat trace or steam trace are two of the most common solutions that have been on the market for almost 60 years. Valve heaters and warmers are also frequently used to prevent valves from freezing.
Heat Trace
Heat trace is wrapped around the valve, and an insulation system is installed over it. Deciding how much heat trace is used can be done in several ways. The most common of these is to use a heat trace design software like Bartec Heloc Pro, or Nelson Design suite.
As the designer inputs data, and calculations are performed to very strict IEE 515 standards, a wattage output is created. Designers will input pipe diameter and length, insulation type, ambient and expected maintain temperatures to name a few data points required.
A couple of the critical inputs are the type and quantity of valves. Flanged, NPT, ball, choke, and gate are many potential options when selecting a valve.
Let’s take a plain 4” ball valve for example:
If we compare the two design softwares above, and input data including a 4” Flanged Ball valve, both softwares will come up and state that approximately 4 ft of 5 watt heat trace is required to keep this valve from freezing. 4 ft x 5 watts per foot = 20 watts. That’s 1/5th of a 100 watt light bulb. It doesn’t take much to maintain temperature as long as the insulation is well maintained.
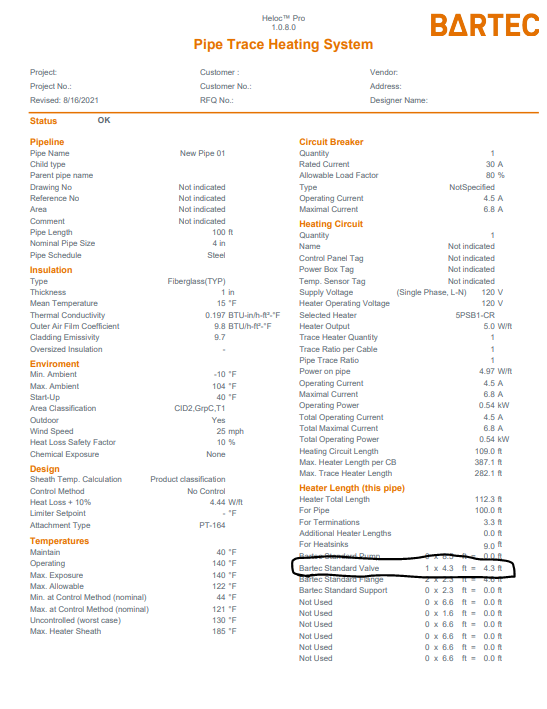
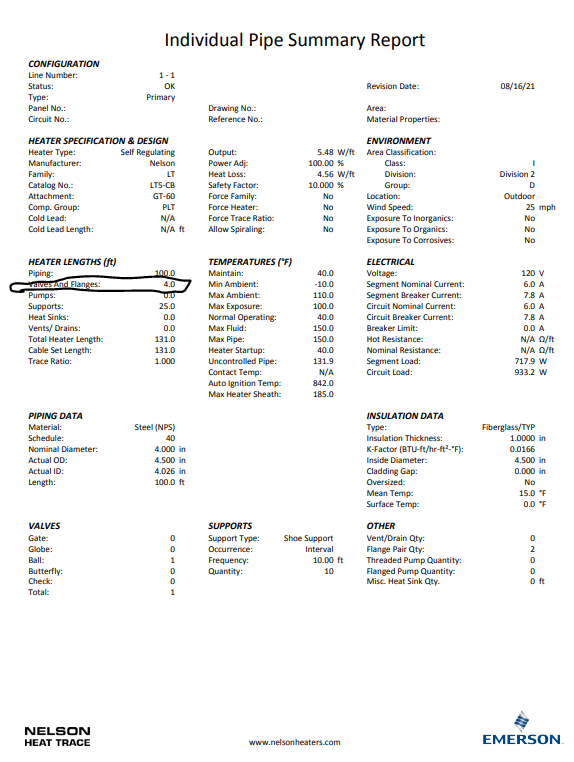
However, problems will arise if the insulation is not regularly maintained and in poor condition, especially when the heat trace is installed the wrong way, or if it is left off after maintenance on the valve is done. Damaged insulation and incorrect installation are the two biggest issues that cause valves to freeze when electric heat trace is chosen as the method to keep them thawed.
Even when installing heat trace for the first time, it’s difficult to put 4 ft of ⅝” wide stiff cable on the body of a valve, and prevent a valve from freezing. Below is a common example of heat trace on a valve:
So even though the IEE 515 calculation software says 4 ft of 5 watt heating cable (or 20 watts) is enough to keep your valve from freezing, how much of the heating cable is really touching the body of the valve? And when maintenance is needed, how easy is it to remove the heat trace to access valves in need of service?
On top of that, when it is time to do maintenance on this valve, the insulation jacket comes off and flops right on the ground (where it often stays for a long time!). The heat trace has to be bent off of the valve, and then you must try to reinstall it just like it was before you started, all while knowing that it will take some time before proper temperatures will be restored to the valve since the insulated cover was off for so long.
Even after all of these considerations there is still something else to think about: this particular valve weighs 83 lbs by itself. Is 20 watts really enough to keep it from freezing? According to the numbers it should be fine, but if the heat source is not actually touching the surface of the valve, heat is not being transferred effectively. And as mentioned before, if the insulation is compromised in any way, all gains in temperature maintenance are lost.
In summary, heat trace often doesn’t provide enough wattage to prevent heat loss and is very difficult to maintain.
Powerblanket Insulated Valve Protection
Installing a 200 watt Powerblanket removable insulation valve cover on this same valve will get you ten times as much heat, while still only pulling 1.6 amps on 120Vac.
Valves generally must remain readily accessible when they need repair/care for an emergency situation. These valves are suitable candidates for removable and disposable insulation cover designs. With Powerblanket removable and insulated valve jackets, the heater is integrated into the valve insulation jacket as a one-piece solution. Pull off the insulation to work on the valve, and both the heater and insulated valve cover come off of the valve. Slip it back on and you are back in business. No hassle, no problem. The same goes for pump insulation jackets, which are very similar to valve insulation jackets.
Powerblanket insulated custom heaters for valves and manifolds are individually designed to fit your pipes and valves perfectly, providing freeze protection down to -40º F / -40º C. Eliminate the need to replace expensive valves and manifolds due to freezing with a system that meets important UL/CSA safety standards and can be customized to operate in C1D2 hazardous locations.
Frequently Asked Questions
What is valve insulation?
Valve insulation involves using removable covers or jackets to wrap around valves, providing a layer of protection that minimizes heat loss and prevents freezing, especially in outdoor or cold environments.
What are the three types of insulation?
The three common types of insulation materials are cellulose, fiberglass, and mineral wool, each offering unique properties for various applications, including valve insulation.
Does an expansion valve need to be insulated?
Yes, insulating an expansion valve is crucial to prevent external temperature influences, ensuring accurate temperature regulation and optimal valve performance.
Powerblanket's equipment boxes keep your valves and manifolds from freezing in even the harshest outdoor environments.