Pouring Concrete in Cold Weather: How Cold is Too Cold?
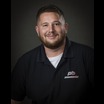
Experts agree that the best temperature to pour concrete is between 50-60 °F. The necessary chemical reactions that set...
Read MoreExperts agree that the best temperature to pour concrete is between 50-60 °F. The necessary chemical reactions that set...
Read MoreWhen it comes to knowing when the best time of year is to conduct construction projects, the weather is god....
Read MoreIt’s time to answer the age-old question: why does road construction take so dang long to complete? Does it really...
Read MoreWhen using gas containers, it’s important to know how gas pressure impacts flow. There are a number of ways you...
Read MoreWinter Road Maintenance Winter Road Construction Typically, it is unwise to do any major structural winter road maintenance in the...
Read More