How Long Does Concrete Take To Set?
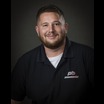
If you really want to know the truth, concrete never stops curing; it continually hardens forever. However, for practical purposes,...
Read MoreIf you really want to know the truth, concrete never stops curing; it continually hardens forever. However, for practical purposes,...
Read MoreWaiting for the curing of concrete can easily test patience, especially when you’re ready to move on to the next...
Read MoreExperts agree that the best temperature to pour concrete is between 50-60 °F. The necessary chemical reactions that set...
Read MoreAn Atypical Concrete Job Concrete curing in freezers is a unique experience. Walk in freezer concrete floor construction requires a...
Read MoreEven the most expertly-placed concrete will wear with age. Unfortunately, this often means cracking. While this is a nearly unavoidable...
Read MoreWe love getting to use our technology for custom applications. One particular company reached out to us with a problem:...
Read MoreHow Warm Does it Have To Be To Pour Concrete? Whether the conditions are hot or freezing, the ideal concrete...
Read MoreHot Weather Concreting Hot weather concreting problems are most often encountered in the summer; however, any condition that increases curing...
Read MoreFirst, let’s define cold weather with respect to pouring concrete. Any time you have three consecutive days where the average...
Read More