Powerblanket Receives Manufacturer of the Year Award from UMA
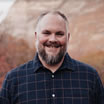
style
Agriculture Barrel Heater Bucket Heater Bulk Material Heater Bulk Material Warmer Business Leadership Composite Curing Composites Concrete Blankets Concrete Insulation Blankets Construction Industry Curing Concrete in Cold Weather Custom Heater Custom Heating Solution Customer Feedback Customization Dairy Freeze Protection Dairy Winter Preparation DEF Tote Heater Drum Heater Drum Warmers Epoxy Epoxy Curing Frac Tank Heaters Freeze Protection Freeze Protection Valve Gas Cylinder Heaters Heated Art Hot Box Industrial Heating Blankets Instrumentation Heaters Insulated Band Heater Pallet Freeze Protection Pallet Heater Pallet Warmer Pipe Heater Process Temperature Control Programmable Logic Controller Propane Tank Heater Space Heaters Specialty Gas Cylinders Heater Specialty Gas Tank Heaters Spray Foam Heater Tank Heater Tote Heaters Valve Heaters Water Tank Freeze Protection Wind Blade Repair
If you haven’t seen this headline somewhere else on the web by now, we’re happy to tell you all about...
Read More