Plant Oil Extraction
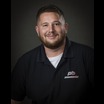
One of the oldest medicinal technologies still in use today is essential oil extraction. The process of removing oils from...
Read MoreOne of the oldest medicinal technologies still in use today is essential oil extraction. The process of removing oils from...
Read MoreCongratulations! You’ve done your research and now understand the benefits of using spray foam insulation vs. old school fiberglass batts....
Read MoreWhen it comes to curing epoxy, nothing is more important than a constant and uniform heat distribution. With a proper...
Read MoreDrum Insulation Blankets From foods to a variety of chemicals and epoxies or resins, proper storage of your industrial materials...
Read MoreIf you’ve dealt with traditional band heaters, then perhaps you have some reservations regarding the usefulness, efficiency, and safety of...
Read MoreViscosity Maintenance With the Proper Heating Solutions Drum heaters and barrel heaters are not only good for the cold months....
Read MoreThe candle industry is on fire, literally and economically. Consumers are not only flocking to sites, stores, and candle parties...
Read MoreWorking in hazardous locations means you have to exercise serious caution regarding procedure, protocol, and equipment usage. What’s more, heating...
Read MoreReducing viscosity is a challenge during cold winter months. Temperatures that dip below optimum working levels can cause materials that...
Read MoreIf you haven’t seen this headline somewhere else on the web by now, we’re happy to tell you all about...
Read MoreIt’s a great question and one I get asked over and over. You would think that such a consistently asked...
Read MoreA curing blanket is a great tool for those who run construction sites during cold weather. While a curing blanket...
Read MorePOWERBLANKET® MOVES TO A 58,000 SQUARE FOOT LOCATION NEXT TO I-15 SALT LAKE CITY – Powerblanket®, provider of superior heat...
Read More