Epoxy Curing For Building Boats and Other Water Craft
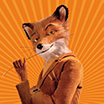
Boat Building Epoxy To many people, summer means time on the lake or in the ocean boating or jet skiing....
Read MoreBoat Building Epoxy To many people, summer means time on the lake or in the ocean boating or jet skiing....
Read MoreEpoxy curing has its challenges. Most resins for composite construction need post curing heat assistance. There are different approaches you...
Read MoreWhen it comes to post curing, maintaining ideal temperature is a must. And if you’re post curing small to medium...
Read MoreCustom orders often have the stigma of being time-consuming and laborious. “How long is that going to take?” we ask...
Read MoreIf you haven’t seen this headline somewhere else on the web by now, we’re happy to tell you all about...
Read More